Neuigkeiten und Projekte
Innovative Methoden für wiederkehrende Prüfungen an Rohrleitungen und Druckbehältern
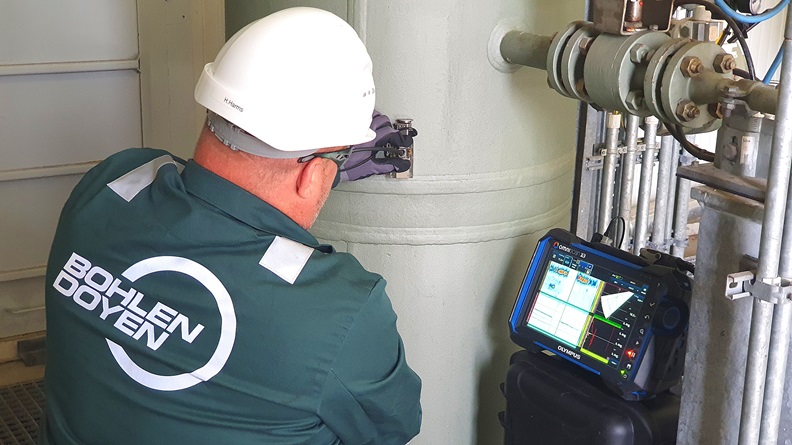
Die gesetzlich vorgeschriebenen, regelmäßigen Prüfungen von Anlagen der Gastechnik sind für jeden Betreiber eine große Herausforderung. Oft sind Prozesse vollständig zu unterbrechen oder sogar ganze Betriebsteile für die Dauer der Kontrollvorgänge stillzulegen. Dadurch ergeben sich neben dem Nutzungsausfall und den entstehenden Kosten der zu entsorgenden Prüfmedien durchaus auch Risiken bei der Wiederinbetriebnahme. Verfahren, bei denen die Anlagen im Betriebszustand bleiben können, sind hierfür eine echte Alternative.
Alle Anlagen- und Leitungsbetreiber sind bestrebt, ihre Rohre, Armaturen und Anlagen nicht nur wirtschaftlich zu betreiben, sondern auch höchste Standards in Bezug auf Umweltschutz, Arbeitssicherheit und Verfügbarkeit zu erfüllen. Daher hat die Bohlen & Doyen Bau GmbH in enger Zusammenarbeit mit dem TÜV NORD eine wegweisende und innovative Lösung weiterentwickelt, um den Nachteilen und Risiken herkömmlicher Prüftechniken von Rohrleitungen und Druckbehältern entgegenzuwirken.
Durch die Nutzung modernster Prüfverfahren wurde eine Lösung konzipiert, welche gleichwohl die Wirtschaftlichkeit und Produktlebensdauer von Anlagen steigern sowie deren Sicherheit und Umweltverträglichkeit gewährleisten kann. Anwendung findet diese neue Technologie bereits bei mehreren Betreibern in der Energiebranche im Bereich der Instandhaltung und Überprüfung.
Die herkömmlichen Prüfverfahren für Druckbehälter und Rohrleitungen umfassen mehrere Schritte, beginnend mit der Außerbetriebnahme des Behälters oder Rohrleitungsteils. Anschließend wird der betroffene Abschnitt entspannt und vom vorhandenen Medium kontrolliert entleert und im Fall von Gasen entsprechend umgepumpt und/oder abgefackelt. Die ursprünglich gastragenden Abschnitte werden danach meist mit Stickstoff gespült, um sie dann gasfreimessen zu können. Im nächsten Schritt wird der Anlagenteil mit Wasser befüllt und einem Drucktest unterzogen. Dabei muss man bedenken, dass der Behälter bzw. Rohrleitungsabschnitt bautechnisch nicht immer für das Auffüllen mit dem Prüfmedium Wasser konstruiert und errichtet wurde. Somit kann es zu erheblichen Standsicherheitsrisiken und statischen Problemen des darunter liegenden Fundaments oder der Behälterstatik kommen.
Alternativ ist ein Abdrücken mit dem Medium Stickstoff möglich, birgt jedoch ein hohes Gefahrenpotenzial. Behälter mit einem Volumen von mehr als 10 m3 sind keine Seltenheit, sodass bei Wasserbefüllung eine zusätzliche Belastung von mehr als zehn Tonnen auf die Anlagenkonstruktion wirkt. Zusammen mit dem Eigengewicht der Anlage ergeben sich oft mehr als 20 Tonnen Last auf das Fundament, welches hierfür erfahrungsgemäß nicht immer ausgelegt ist und zu erheblichen Gefährdungen für die Anlagensicherheit führen kann. Zusätzlich besteht die Möglichkeit, dass das Prüfwasser Korrosion verursacht. Dies führt auf lange Sicht zu Schäden an den Innenoberflächen des Behälters bzw. der Rohrleitung. Nachdem die Druckprüfung mit dem Prüfmedium Wasser erfolgt ist, wird dieses aus dem Prüfobjekt abgeführt und unter großem Aufwand und hohen Kosten entsorgt. Der Behälter bzw. der Leitungsabschnitt muss dann aufwendig getrocknet und wieder angebunden werden. Abschließend folgt die Inbetriebnahme des Prüfobjektes.
Konventionelle Prüfverfahren: nicht nur kostenintensiver, sondern auch risikoreicher
Unter dem Aspekt der erläuterten Prozessschritte im Zuge einer Prüfung von Druckbehältern und Rohrleitungsabschnitten ergeben sich für diese herkömmlichen Verfahren große Nachteile. Sie sind oft mit hohen Kosten und einem erheblichen Zeitaufwand verbunden. Unterschätzt werden zuweilen auch die Risiken, die sich im Verlauf entsprechender Prüfarbeiten ergeben können. Neben der Standsicherheit entstehen Risiken auch durch die Entsorgung des Prüfmediums oder das Abfackeln des Betriebsmediums. Daneben besteht schließlich ein nicht unerheblicher Aufwand durch die Beschaffung von Prüfmaterialien und Hilfsmitteln wie Gerüsten, Kränen, mobile Fackeln, mobile Verdichtern, Prüfwasser, Stickstoff und Dichtungen.
Für die Arbeitssicherheit bestehen ebenfalls besondere Herausforderungen, da teilweise das Personal mit Atemschutz zu arbeiten hat und die Durchführung der Prüfung hohen Gefährdungen ausgesetzt ist. Das Abbauen von Rohrkomponenten oder -verbindungen erfordert zusätzliche Arbeitszeit und -kosten, wodurch die Wartungsarbeiten komplizierter werden und sich die notwendigen Betriebsunterbrechungen verlängern.
Somit ist eine Alternative zur Durchführung von konventionellen Prüfverfahren an Rohrleitungen und Druckbehältern damit auch aus nachhaltiger Sicht absolut sinnvoll. Ein Verfahren für gesetzlich vorgegebene Prüfungen von Rohrleitungen und Druckbehältern, die sich in Betrieb befinden, ist also auch aus Sicht der Effizienz und Ressourcenschonung vorzuziehen. Neben einer nachhaltigeren Prozessabwicklung ergibt sich dann auch eine steigende Anlagenlebensdauer.
Durch die neue Fassung der BetrSichV gelten seit 2015 geänderte Regelungen für die Druckbehälteranlagenprüfung. Diese sehen alle fünf Jahre eine innere Prüfung und alle zehn Jahre eine Festigkeitsprüfung vor. In diesem Zeitraum muss die gesamte Anlage untersucht werden. Durch die Betriebssicherheitsverordnung besteht die Möglichkeit, ein spezifisches Konzept zur Prüfung eines Behälters zu erstellen. Hierdurch können durch Berücksichtigung definierter Parameter, die innere und die Festigkeitsprüfung ersetzt werden. Wird ein gleichwertiges Prüfkonzept vorgelegt, ist es möglich, die wiederkehrenden Maßnahmen auszuführen, ohne den Behälter zu öffnen oder die Anlage außer Betrieb zu nehmen. Auf dieser Grundlage ist es möglich, die Entleerung, Gasfreimessung, Reinigung und die Entsorgung mit einem geeigneten Prüfverfahren einzusparen. Die jeweilige Methodik kann auch für die wiederkehrenden Prüfungen an Rohrleitungen und Segment- oder Scholzverschlüssen angewendet werden. So kann die Integration modernster Sicherheitstechnologien und -verfahren eine erhöhte Anlagensicherheit und -verfügbarkeit gewährleisten. Potenzielle Sicherheitsrisiken lassen sich dabei frühzeitig identifizieren bzw. beheben oder es können präventive Maßnahmen implementiert und eingeleitet werden.
Durch kontinuierliche Überwachung und Analyse während des Betriebs werden potenzielle Probleme frühzeitig erkannt und behoben. Dies führt zu einer verbesserten Anlagenleistung und einer Reduzierung von Stillstandzeiten.
Neues Prüfverfahren mit effektiverer Ultraschalltechnik
Die Grundlage für die Erstellung des innovativen Prüfkonzeptes sind hochauflösende Ultraschallverfahren wie „Phased Array“ und der „Time of Flight Diffraction“ (TOFD“)-Methode. Das Phased Array Ultrasonic Testing (PAUT) ist eine fortschrittliche Technik, die in der Schweißnahtprüfung weit verbreitet ist. Sie ermöglicht eine gründliche und genaue Untersuchung von Schweißnähten, um Defekte wie Risse, Poren oder Inhomogenitäten zu identifizieren, welche die strukturelle Integrität beeinträchtigen könnten.
Im Gegensatz zu herkömmlichen Ultraschallprüfmethoden verwendet PAUT spezielle Ultraschallsonden mit einer Reihe von kleinen, individuell ansteuerbaren Elementen. Diese Elemente erzeugen Ultraschallwellen, die durch Phasensteuerung präzise gerichtet und fokussiert werden können. Durch die Anpassung der Phasen der einzelnen Elemente kann der Ultraschallstrahl elektronisch gelenkt und fokussiert werden, um verschiedene Bereiche der Schweißnaht zu überprüfen. Dies ermöglicht eine gezielte Untersuchung und Lokalisierung potenzieller Defekte. Ein weiterer Vorteil ist die Fähigkeit, mehrere Prüfwinkel gleichzeitig abzudecken, was die Inspektionszeit verkürzt und die Effizienz erhöht. Darüber hinaus bietet PAUT eine höhere Auflösung und Empfindlichkeit im Vergleich zu herkömmlichen Methoden, was eine präzisere Charakterisierung von Defekten ermöglicht.
Die TOFD-Prüfung verwendet zwei Ultraschallwandler, einen Sender, der einen kurzen Ultraschallimpuls erzeugt und einen Empfänger, der die Impulse von defekten reflektierten Ultraschallwellen erfasst. Die Zeit, die die Ultraschallwellen benötigen, um von einem Sender zu einem Empfänger zu gelangen, wird gemessen. Diese Zeit wird als Time of Flight bezeichnet und hängt von der Materialdicke und der Lage des Defekts ab. Durch die Analyse der TOFD-Daten lassen sich verschiedene Defekte wie Risse, Poren oder Volumenveränderungen in der Schweißnaht genau lokalisieren und charakterisieren. Die hohe Empfindlichkeit und Genauigkeit von TOFD machen es zu einer bevorzugten Methode in Branchen wie dem Schiffbau, der Luft- und Raumfahrt sowie der Öl- und Gasindustrie. TOFD bietet mehrere Vorteile, darunter eine schnelle Inspektion mit hoher Auflösung und Genauigkeit sowie die Möglichkeit, präzise Tiefenmessungen durchzuführen. Darüber hinaus ermöglicht TOFD eine vollständige Abdeckung der Schweißnaht ohne tote Zonen, was die Zuverlässigkeit der Inspektion erhöht.
Anwendungsvoraussetzungen durch die BetrSichV vorgegeben
Ein Anwendungsfeld für den Einsatz des Prüfkonzeptes erfolgt bei Bohlen & Doyen in Absprache mit dem TÜV NORD im Bereich der oberirdischen Rohrleitungs- und Druckbehälterprüfung. Die BetrSichV legt klare Anforderungen für den sicheren Betrieb von Anlagen und Rohrleitungen fest. Grundsätzlich sind die Leitungs- und Anlagenbetreiber dazu verpflichtet, ihre Rohrleitungen regelmäßig auf Sicherheit und Funktionalität zu prüfen. Insbesondere für Unternehmen, die mit Druckbehältern und Rohrleitungen arbeiten, ist die Implementierung von Prüfprogrammen von entscheidender Bedeutung, um die Sicherheit zu gewährleisten und gesetzliche Vorgaben einzuhalten.
Nach der geltenden BetrSichV haben Betreiber und Verantwortliche einen gewissen Spielraum bei der Auswahl von geeigneten Prüfmethoden und -techniken. Dies kann visuelle Inspektionen, Druckprüfungen, Ultraschalltests und andere zerstörungsfreie Verfahren umfassen. Alle sind am Ende auf die spezifischen Eigenschaften der Prüfkörper, auf die Betriebsbedingungen und die gesetzlichen Anforderungen zugeschnitten. Die Durchführung der Inspektionen, der Tests und der Wartungsarbeiten ist jeweils die Voraussetzung, um potenzielle Risiken zu identifizieren und zu minimieren. Dabei sind die regelmäßigen Prüf- und Wartungsarbeiten gemäß BetrSichV ordnungsgemäß zu dokumentieren.
Die beteiligten Unternehmen sind dazu verpflichtet, genaue Aufzeichnungen über durchgeführte Arbeiten zu führen und Ergebnisse sowie festgestellte Mängel entsprechend festzuhalten. Diese Dokumentation dient nicht nur der gesetzlichen Einhaltung, sondern dann auch der Reproduzierbarkeit der vorangegangenen Prüfungen. Eine wesentliche Komponente bei der Entwicklung solcher individuellen Prüfprogramme für Rohrleitungen ist die Risikobewertung. Hierbei werden potenzielle Gefahrenquellen ermittelt und die möglichen Auswirkungen von Fehlfunktionen in einer Gefährdungsbeurteilung bewertet. Basierend auf dieser Bewertung werden angemessene Prüfintervalle festgelegt, um sicherzustellen, dass sich die Rohrleitungen ordnungsgemäß warten und überprüfen lassen.
Die Technik bietet eine verbesserte Genauigkeit, da sie zahlreiche Signale auf einmal erfasst und damit auch die Anzahl der Fehldiagnosen reduziert.
Durchführung
Die Möglichkeit einer prozess- und produktionsbegleitenden Prüfung ist ein zentraler Bestandteil des Ansatzes von Bohlen & Doyen, um die Wirtschaftlichkeit von Anlagen zu steigern. Durch kontinuierliche Überwachung und Analyse während des Betriebs werden potenzielle Probleme frühzeitig erkannt und behoben. Dies führt zu einer verbesserten Anlagenleistung und einer Reduzierung von Stillstandzeiten. Darüber hinaus tragen die technischen Methoden zur Schonung von Ressourcen und zur Verminderung von Umweltrisiken bei.
Die Einhaltung von Energie- und Umweltmanagementstandards wie der DIN EN ISO 50001 und DIN EN ISO 14001 sowie der vorgegebenen CO2-Bilanz des DEHSt (Deutsche Emissionshandelsstelle) wird durch effiziente Prozesse und innovative Technologien sichergestellt. Die Erstellung und Umsetzung des innovativen Prüfkonzepts für Druckbehälter und Rohrleitungen erfolgt in mehreren Schritten. Zunächst werden die Behälterdokumentationen und die dazugehörige Gefährdungsbeurteilung intensiv geprüft und bewertet, um potenzielle Schwachstellen an den sich im Betrieb befindlichen Anlagen zu identifizieren und eine umfassende Analyse zu erstellen. Anschließend erfolgt in enger Abstimmung mit dem Betreiber und der zugelassenen Überwachungsstelle (ZÜS) die Festlegung eines geeigneten Prüfverfahrens. In den meisten Fällen beinhaltet dies eine Ultraschallprüfung und eine Oberflächenrissprüfung der hochbelasteten Nähte der Anlage. Das Scannen des Materialvolumens sowie der Schweißnähte mittels einer Phased-Array-Prüfung erfolgt durch speziell geschultes und zertifiziertes Fachpersonal. Dabei wird der Prüfkopf entlang der identifizierten Schwachstellen geführt und das Materialvolumen dreidimensional digital erfasst.
Das Phased-Array-Verfahren hat gegenüber den konventionellen Ultraschallprüfsystem die Vorteile der einfacheren Bedienbarkeit, der höheren Prüfgeschwindigkeit und der besseren Sicherheit. Ein Phased-Array-Prüfkopf ist deutlich robuster und einfacher zu handhaben als herkömmliche Einzelelementprüfköpfe. Die Technik bietet eine verbesserte Genauigkeit, da sie zahlreiche Signale auf einmal erfasst und damit auch die Anzahl der Fehldiagnosen reduziert.
PAUT-Prüfstrategien lassen sich zusätzlich optimieren, indem sie zusammen mit der Simulation verwendet werden. Die Phased-Array-Technik liefert eine dauerhafte Aufzeichnung, erzeugt keine radioaktive Strahlung und lässt sich für mehrere Anwendungen einsetzen. Damit werden Defekte nicht nur an der Oberfläche, sondern auch im Volumen einer Schweißnaht erkannt. Somit gibt es auch Informationen über die seitliche Position eines Defekts (Tiefe und Höhe). Selbst kleine Fehlstellen, die zu einem Materialversagen führen könnten, werden durch dieses hochauflösende Ultraschallverfahren erfasst, sodass eine abschließende und sehr zuverlässige Bewertung der Integrität des Prüfobjektes gewährleistet werden kann. Als innovative Prüfmethode wird sie zur Identifizierung von Diskontinuitäten eingesetzt, um die Materialintegrität zu bestimmen.
Fazit und Ausblick
Das zerstörungsfreie Prüfverfahren der Phased-Array-Technik ermöglicht eine hochaufgelöste und präzise Diagnose des Materialzustandes an Druckbehältern und Leitungen, ohne diese außer Betrieb nehmen zu müssen. Dabei ermöglicht die reproduzierbare Ergebnisdokumentation von Bohlen & Doyen eine fundierte Planung und Durchführung von Instandhaltungsmaßnahmen. Diese wiederum verbessern die Planungssicherheit und die Effizienz der Wartungs- und Reparaturprozesse. Es ergibt sich zudem ein Mehrwert für die Betriebsführung von Anlagen durch die frühzeitige Erkennung von Schäden und Fehlstellen ohne das Öffnen des Behälters oder Rohrleitungsabschnittes.
In Zukunft wird auch Wasserstoff als Medium immer mehr Bereiche erschließen. Leider stellt die wasserstoffinduzierte Korrosion eine besondere Bedrohung für die Integrität von Anlagen dar, insbesondere beim Betrieb von Behältern und Rohrleitungen. Diese Art der Korrosion kann zu schwerwiegenden Schäden führen, die nicht nur die Sicherheit gefährden, sondern auch erhebliche finanzielle Verluste und Umweltschäden mit sich bringen. Wasserstoffinduzierte Korrosion tritt auf, wenn Wasserstoff in das Material eindringt und dort Reaktionen auslöst, die zu Versprödungen des Materials mit der Folge von Rissbildungen und schließlich dem Versagen des Materials führen. Dies kann insbesondere bei metallischen Werkstoffen auftreten, die in Kontakt mit wässrigen Medien stehen, wie z. B. in Druckbehältern und Rohrleitungen, die für den Transport von Flüssigkeiten verwendet werden. Die Auswirkungen der wasserstoffinduzierten Korrosion können folglich verheerend sein und reichen von lokaler Oberflächenbeschädigung bis hin zu schweren strukturellen Schäden wie Undichtigkeiten und im schlimmsten Fall zu Brüchen. Dies stellt nicht nur eine Gefahr für die Sicherheit von Mitarbeitern und der Öffentlichkeit dar, sondern birgt auch die Gefahr für erhebliche Betriebsunterbrechungen und finanzielle Verluste.
Es besteht folglich das Bestreben, die Ursache der wasserstoffinduzierten Korrosion frühzeitig zu erkennen und zu überwachen bzw. Gegenmaßnahmen zu ergreifen. Mit herkömmlichen Prüfverfahren ist dies jedoch kaum zu realisieren, sodass erst spät, in einem fortgeschrittenen Stadium, die Fehlstellen erkannt und lokalisiert werden können. Insgesamt bleibt das Thema der wasserstoffinduzierten Korrosion ein fortlaufender Prozess, der eine enge Zusammenarbeit zwischen Unternehmen, Regulierungsbehörden und Technologieanbietern erfordert. Der Einsatz modernster Prüfverfahren mit der Weiterentwicklung von Techniken und Systemen durch Unternehmen wie Bohlen & Doyen, gemeinsam mit dem TÜV NORD, kann dazu beitragen, Risiken und Schäden zu minimieren und eine sicherere und nachhaltigere Zukunft für die Industrie zu schaffen.
Die Zukunft der Prüfung von Druckbehältern und Rohrleitungen wird von einer zunehmenden Integration innovativer Technologien, einer verstärkten Datenanalyse sowie einer kontinuierlichen Verbesserung der Materialien und Standards geprägt sein.
Autoren
Holger Harms
Bernd Saathoff
Bohlen & Doyen Bau GmbH
Hauptstr. 248
26639 Wiesmoor
Tel.: +49 (0) 4944 9456 251
h.harms_at_bohlen-doyen.com
www.bohlen-doyen.com
Thorsten Jacobs
TÜV NORD Systems GmbH & Co. KG
Große Bahnstr. 31
22525 Hamburg
Tel.: +49 (0) 160 888 4116
tjacobs_at_tuev-nord.de
www.tuev-nord.de
Veröffentlicht in
bbr – Juniausgabe 2024